Speed Up Your Lead Times with Quick Turn
RAF Electronic Hardware Products
Threaded Inserts for Plastic Now Available: RAF now offers brass threaded inserts for plastics. Formerly Tri-Star threaded inserts, we offer parts in brass, stainless steel, and more. Shop now or contact us to request a quote.
New NAS hardware parts: In addition to our online products, we have also added over 50 new NAS parts to our inventory.
See the full list of new parts here, or contact us to request a quote.
Shop Online with Your RAF Account
Log in to your RAF account for access to exclusive tools. By logging in, you have the ability to access your distributor pricing, shop and buy products online instantly, reorder parts you previously purchased, view tracking details for current orders, and view your order history. Watch the overview below for details.
Check RAF Stock
Download Our Catalogs & Product Information
-
Browse our online catalogs for details on our SAE and metric dimensioned components for distributors and customers. Our RAF catalog has information on over 45,000 stock part numbers that offer same-day processing and shipping.
-
View our threaded inserts catalog for details on brass, stainless steel, and other threaded inserts. Threaded inserts are generally used for plastics, and were formerly offered by Tri-Star Industries.
-
The Harmonized Commodity Description and Coding System, also known as the Harmonized System (HS) of tariff nomenclature is an internationally standardized system of names and numbers to classify products. Find the harmonized fastener codes for more details on our products.
Tri-Star Inserts Are Now RAF Inserts
Threaded Inserts for Plastics
RAF now offers threaded inserts for plastics. Formerly offered by Tri-Star Industries, our threaded inserts come in a wide variety of sizes, styles, and materials. Our most popular option, brass threaded inserts for plastics, are used to help strengthen screw connections. Shop our full selection online or contact us to request a quote for custom a custom insert.
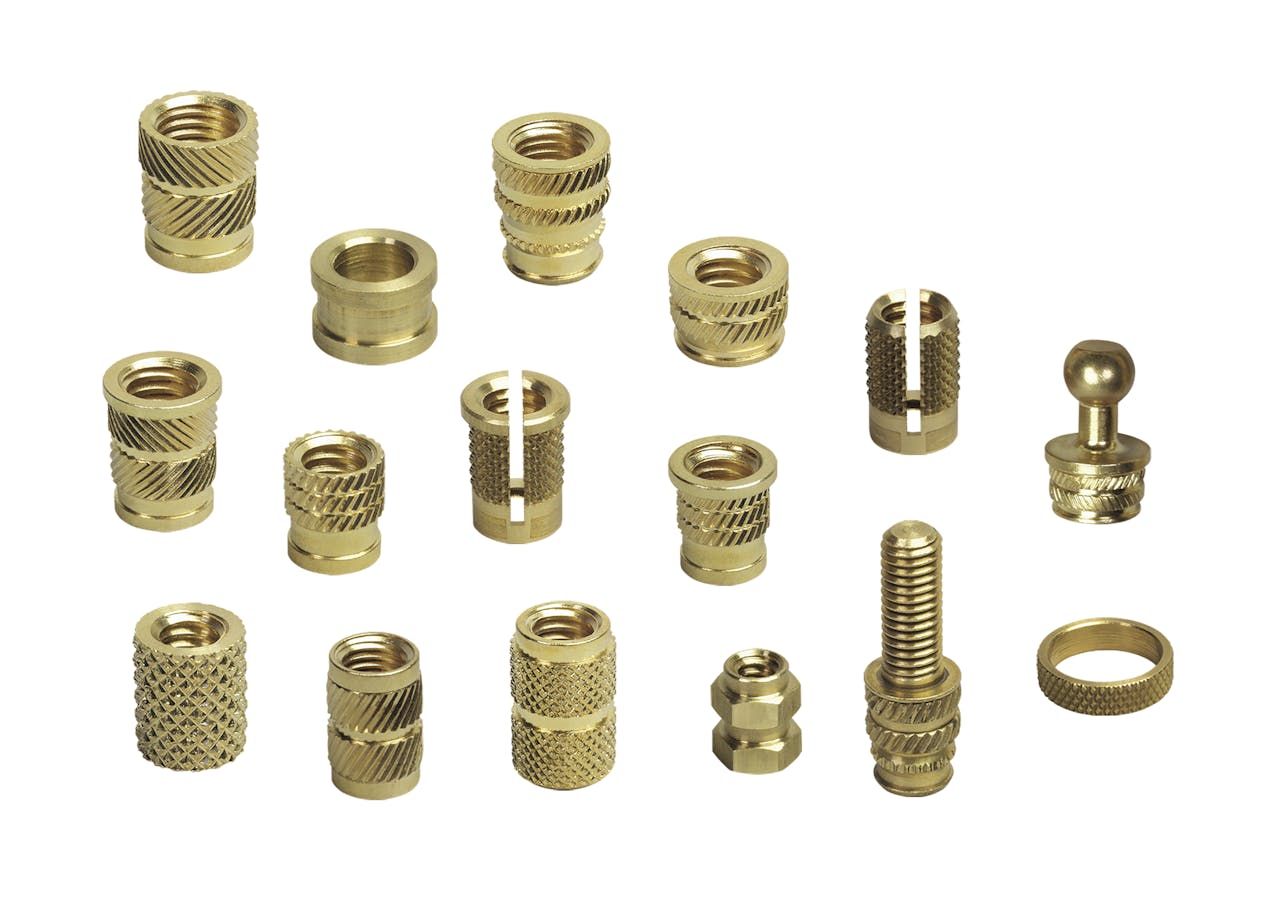
Quick Turn Delivery
RAF has a dedicated manufacturing cell with equipment that can deliver select products to you in days or weeks, depending on your needs. Products include standoffs, spacers, male-females, swage, male-male, and modified parts, available in all materials except nylon. Quantities are limited to 2,000 pieces.
Not only do we deliver our products efficiently, with the best customer service, we take pride in our quality and adhere to all requirements, standards, and compliances. Contact us for more information on our quick turnaround service.
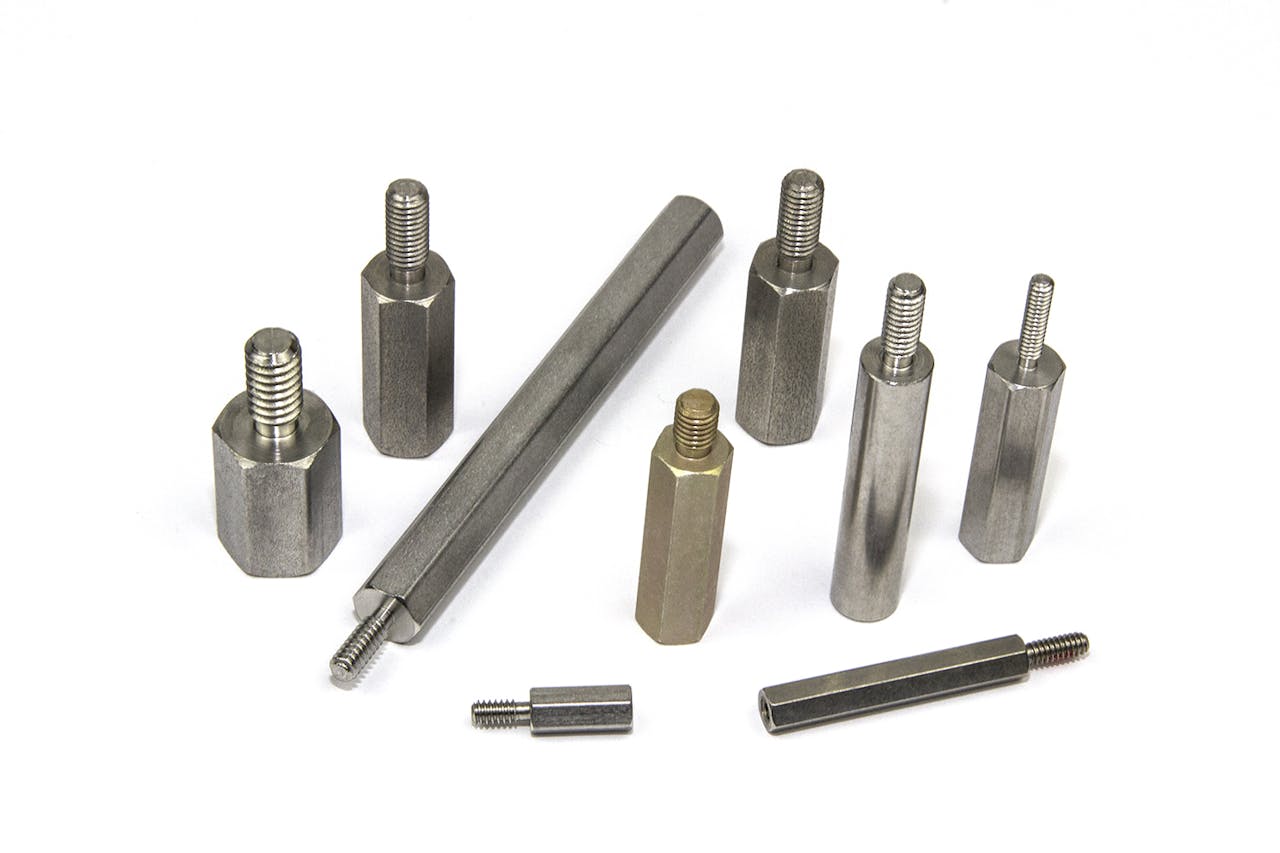
High Precision, Tight Tolerance Products
RAF offers precision machining for an array of applications and industries with exceptional attention to detail and quality. Our precision machined components are available in a variety of materials including various grades of beryllium copper, brass, stainless steel, steel, and aluminum.
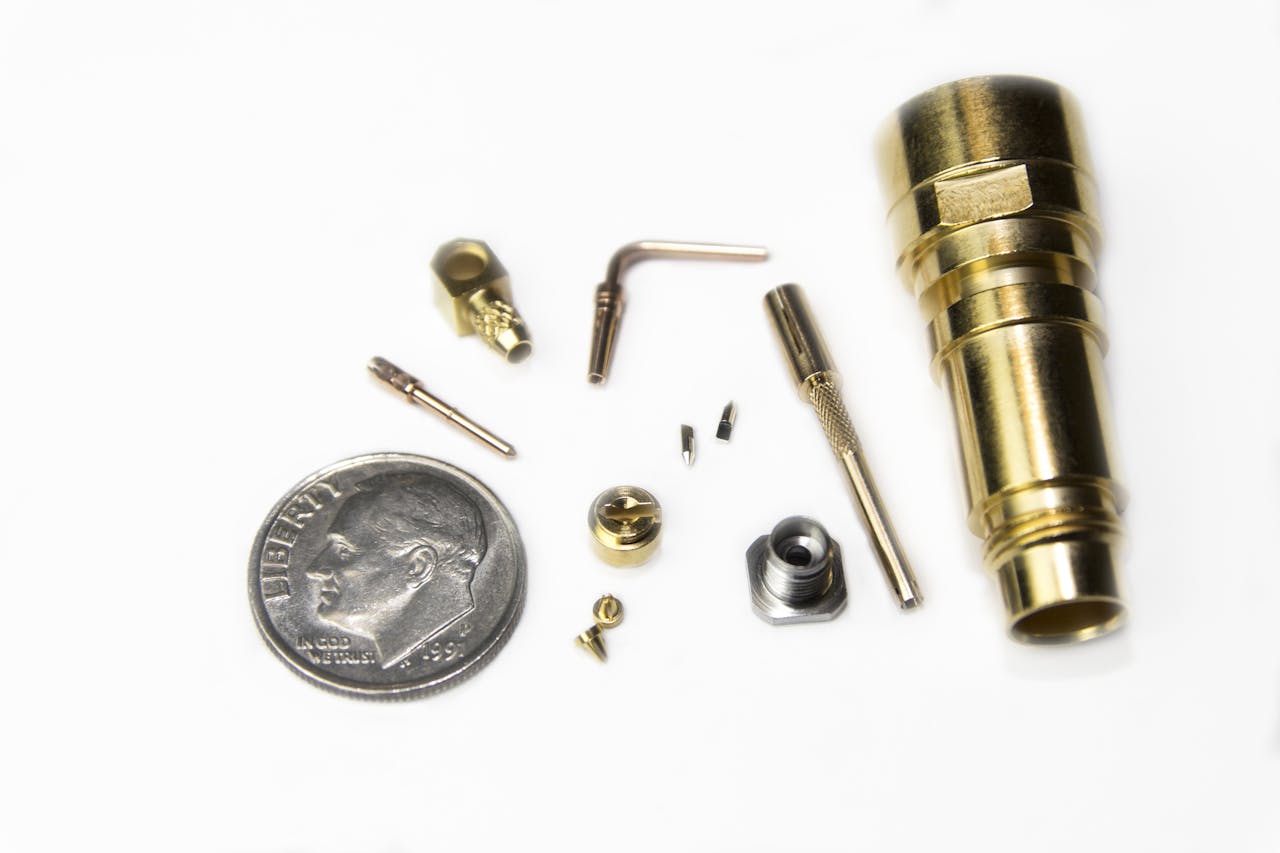
Customize Parts for Your Application
Precision Machining & Engineering Support
RAF’s expert staff provides complete engineering support for your custom part needs, including everything from electrical contacts to precision screws. We support short runs and prototypes, offer turned diameters from .010” to .750”, and tolerance on diameters to +/.0002”. We also provide in-house beryllium copper heat treatment, tooling, and a state-of-the-art plating facility. Get in touch with us for more information on our custom manufacturing capabilities.
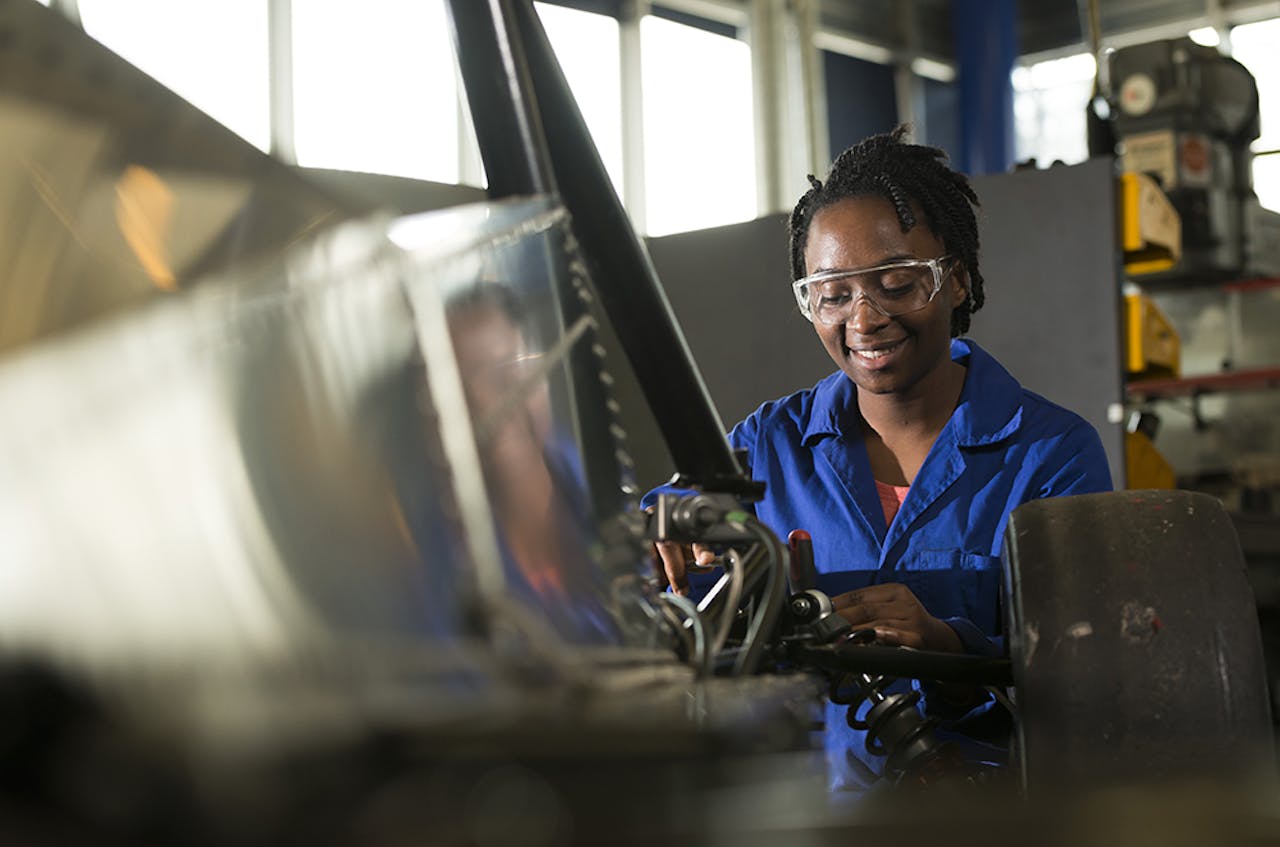